GST on Cement Industry
- 16 Sep 24
- 14 mins
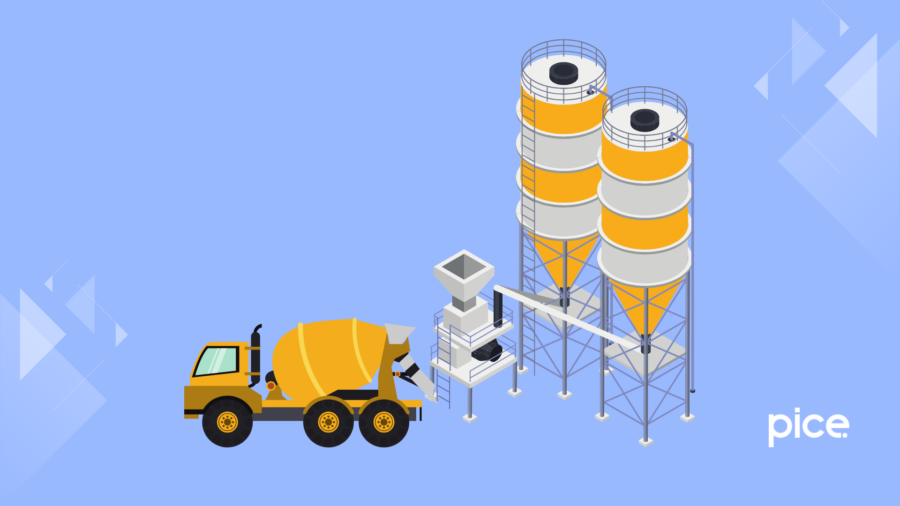
GST on Cement Industry

Key Takeaways
- The 28% GST rate on cement has significantly increased the cost of production and pricing in the market.
- GST has simplified tax compliance but also introduced challenges with higher costs in the cement sector.
- Transportation and warehousing efficiencies have improved under GST, reducing logistical bottlenecks for cement manufacturers.
- Input Tax Credit (ITC) management is crucial for cement companies to optimize costs under the GST regime.
- The high GST rate on cement affects affordability in the real estate and infrastructure sectors.
The introduction of the Goods and Services Tax (GST) in India has significantly impacted various industries, including the cement industry. As one of the key building materials in the infrastructure sector, cement plays a critical role in the development of housing, commercial spaces, and large-scale infrastructure projects. Understanding the implications of GST on cement is essential for all stakeholders, including cement manufacturers, real estate developers, and the logistics industry.
What is GST on Cement?
The GST on cement is currently pegged at 28%, which is one of the higher tax rates within the GST framework. Cement is categorized under the highest tax slab because it is deemed a luxury item, despite its crucial role in the infrastructure and housing industries. The 28% rate on cement is applied uniformly across different types of cement, including grey cement, white cement, and Super Sulphate cement. This high tax rate has direct implications on the cost of cement production, influencing the overall pricing structure in the market.
💡 If you want to pay your GST with Credit Card, then download Pice Business Payment App. Pice is the one stop app for all paying all your business expenses.
Cement manufacturers have had to adjust their pricing strategies to accommodate this tax structure, leading to an upward pricing trend in the cement industry. This increase in prices has a cascading effect on the cost of construction for real estate developers, especially in the affordable housing and luxury housing categories. The demand for cement remains high, driven by the continuous growth in infrastructure projects, but the high GST rates have raised concerns about the sustainability of current pricing trends.
Furthermore, the clean energy cess, which was imposed on coal (a primary fuel for cement production), is still applicable under the GST regime, adding to the overall cost of production. The tax regime has also introduced complexities in managing input tax credits (ITC) for cement producers, making it crucial for companies to have efficient supply chain management systems to optimize costs.
Under the VAT Regime
Before the introduction of GST, the Value Added Tax (VAT) system was in place, which had a different tax structure for the cement industry. Under the VAT regime, cement was subject to multiple taxes, including Central Excise Duty, VAT, and additional state levies. The tax rates varied from state to state, leading to operational inefficiencies and complexities in the tax regime. Cement companies had to navigate through a maze of duties applicable at different stages of production and distribution, which often resulted in increased costs for infrastructure projects.
The previous tax regime had its own set of challenges, particularly in terms of compliance. Cement manufacturers had to deal with a complex web of tax components, including duties on limestone quarrying, transportation costs, and excise duties on various forms of cement. This fragmented tax structure led to higher costs for infrastructure development and real estate industries, as the cumulative tax burden was significant.
The VAT regime also had a direct impact on the pricing of cement, as companies for limestone quarrying and cement production had to factor in multiple taxes while determining their final prices. Additionally, the lack of uniformity in tax rates across states resulted in price disparities, making it difficult for cement companies to maintain consistent pricing strategies across different regions.
The pre-GST regime, despite its flaws, allowed some degree of flexibility for cement producers in terms of availing input credits. However, the cumbersome process and the time-consuming compliance requirements often negated the benefits of such credits, leading to higher operational costs.
Impact of GST on Cement Industry
Transportation Cost
The introduction of GST has brought about significant changes in the logistics and transportation sector, which directly impacts the cement industry. One of the positive impacts of GST is the reduction in transit time and turnaround times at checkpoints, as the implementation of GST has led to lesser compliances and a more streamlined process for goods movement. This reduction in costs for transportation has been a sigh of relief for cement manufacturers, who previously faced delays and higher costs due to the complexities in the tax regime.
However, the high GST rates on cement still pose a challenge for cement bag transportation, as the overall cost of transportation remains a significant component of the final price of cement. The demand for logistics services has increased with the growth of the infrastructure sector, and the logistics industry has had to adapt to the new tax regime to ensure efficient supply chain management.
Warehousing
The impact of GST on warehousing in the cement industry is multifaceted. On one hand, the consolidation of warehouses has become more viable due to the removal of state-specific taxes, leading to a more efficient distribution network. On the other hand, the increased GST rates have contributed to higher warehousing costs, as cement producers need to factor in the tax when calculating the overall cost of production.
The warehousing of cement, especially in bulk form, is crucial for managing inventory and ensuring a steady supply to meet the demand for cement in the infrastructure industry. The GST regime has enabled better management of cement warehouses, but the increased tax burden has also led to higher operational costs for cement companies.
Increased Component Costs
The GST regime has led to an increase in the cost of various components involved in cement production, such as limestone quarries, clinker production, and transportation. The cumulative effect of higher GST rates and the clean energy cess has resulted in increased costs for cement producers, which has, in turn, affected the overall cost of cement.
Cement manufacturing companies like Ultratech Cement Ltd. have had to navigate these challenges by optimizing their supply chain management and exploring ways to reduce operational inefficiencies. However, the increased cost of components continues to be a significant factor in the pricing of cement, impacting the profitability of cement manufacturing companies and the cost of construction for infrastructure projects.
GST Calculation on Cement
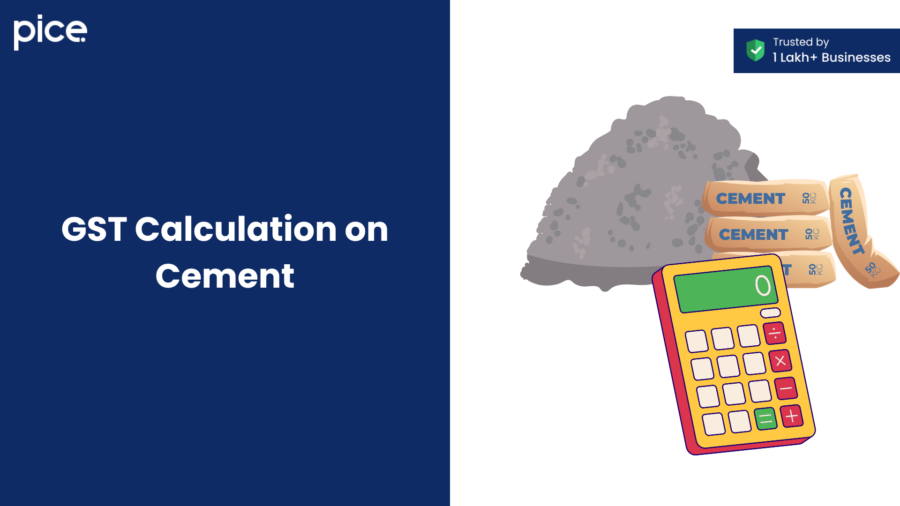
The calculation of GST on cement involves applying the standard rate of GST, which is 28%, to the ex-factory price of cement. This rate is applied uniformly across different types of cement, such as grey cement, white cement, and super sulphate cement, regardless of the form in which the cement is sold (bulk or bagged). The GST is added to the ex-factory price, and the total becomes the final price that customers have to pay.
In addition to the standard GST rate, cement manufacturers also have to account for the clean energy cess on coal and other raw materials used in cement production. This cess, along with the GST, forms the total tax burden on cement, which is then passed on to the end consumers.
The availability of input tax credits (ITC) under the GST regime is one of the key factors that can help in reducing the overall tax burden for cement manufacturers. However, the process of claiming ITC can be complex, requiring meticulous documentation and compliance with GST rules. Proper management of ITC can lead to significant savings for cement producers, but any lapses in compliance can result in penalties and loss of credits.
Impact of GST on Cement Manufacturing Companies
The introduction of GST has had a profound impact on cement manufacturing companies in India. On one hand, the uniform tax structure has simplified the tax compliance process, reducing the number of duties applicable and making it easier for companies to manage their tax liabilities. This has led to a reduction in operational inefficiencies and provided a more predictable business environment for cement manufacturers.
However, the high rate of GST on cement, coupled with the clean energy cess, has led to an increase in the cost of production. Cement companies have had to pass on these increased costs to the consumers, leading to higher prices for cement in the market. This has had a direct impact on the affordability of construction projects, particularly in the affordable housing and infrastructure sectors.
Cement manufacturing companies have also had to invest in better supply chain management systems to ensure compliance with GST rules and optimize their operations. The increased focus on efficiency has led to some positive outcomes, such as better management of inventory and reduced turnaround times. However, the overall impact of GST on cement manufacturing companies has been mixed, with the benefits of a simplified tax structure being offset by the challenges posed by high tax rates and increased costs of production.
Current GST Trends and Real Estate Industry
The real estate industry has seen a mixed impact of GST, particularly with regard to the demand for cement and the overall cost of construction. The high GST rates on cement have contributed to an increase in the cost of construction, which has been a point of concern for real estate developers. This increase in costs has been particularly challenging for developers in the affordable housing category, where margins are already thin.
However, the uniform tax structure under GST has also led to some positive impacts on the real estate sector. The removal of multiple taxes and the availability of input tax credits have simplified the tax compliance process for real estate developers, leading to lesser time spent on managing tax-related issues and more focus on core business activities. The reduction in costs associated with logistics and warehousing has also been a positive outcome of the GST regime, as real estate developers can now manage their supply chains more efficiently.
The current trends in the real estate sector indicate a growing demand for infrastructure projects, which in turn drives the demand for cement. However, the upward pricing trend in the cement industry, driven by high GST rates, remains a challenge that needs to be addressed to ensure the sustainability of the real estate sector in the long run.
ITC on the Cement Industry
The availability and management of Input Tax Credit (ITC) under the GST regime play a crucial role in the financial health of the cement industry. ITC allows cement manufacturers to offset the taxes paid on inputs against their output tax liabilities, leading to a reduction in the overall tax burden. However, the process of claiming ITC is fraught with challenges, particularly due to the complexities in documentation and compliance with GST rules.
Cement producers need to ensure that their supply chain management systems are robust enough to track and manage ITC claims effectively. Any lapses in compliance can lead to the denial of ITC, resulting in higher costs of production. The management of ITC is particularly important for large cement manufacturing companies like Ultratech Cement Ltd., which have extensive operations and multiple points of tax incidence.
The impact of ITC on the cement industry is significant, as it directly affects the profitability of cement companies and the pricing of cement in the market. Proper management of ITC can lead to cost savings and improved margins, while any inefficiencies in ITC management can have a negative impact on the financial performance of cement manufacturers.
In conclusion, while the GST regime has brought about several positive changes in the tax structure and compliance processes for the cement industry, the high tax rates and the complexities in managing ITC remain significant challenges. Cement manufacturing companies need to focus on optimizing their operations and supply chain management to navigate these challenges and maintain their competitiveness in the market. The real estate sector, which is a major consumer of cement, also needs to adapt to the changing tax landscape to ensure the sustainability of infrastructure development in India.